«Bringing Artificial Intelligence into mechanics»
01.07.2025Since 2024, Hamilton’s prototyping team has been leveraging AI-powered cost estimation – delivering precise quotes within minutes, streamlining processes, and creating more time for what really matters: technical implementation.
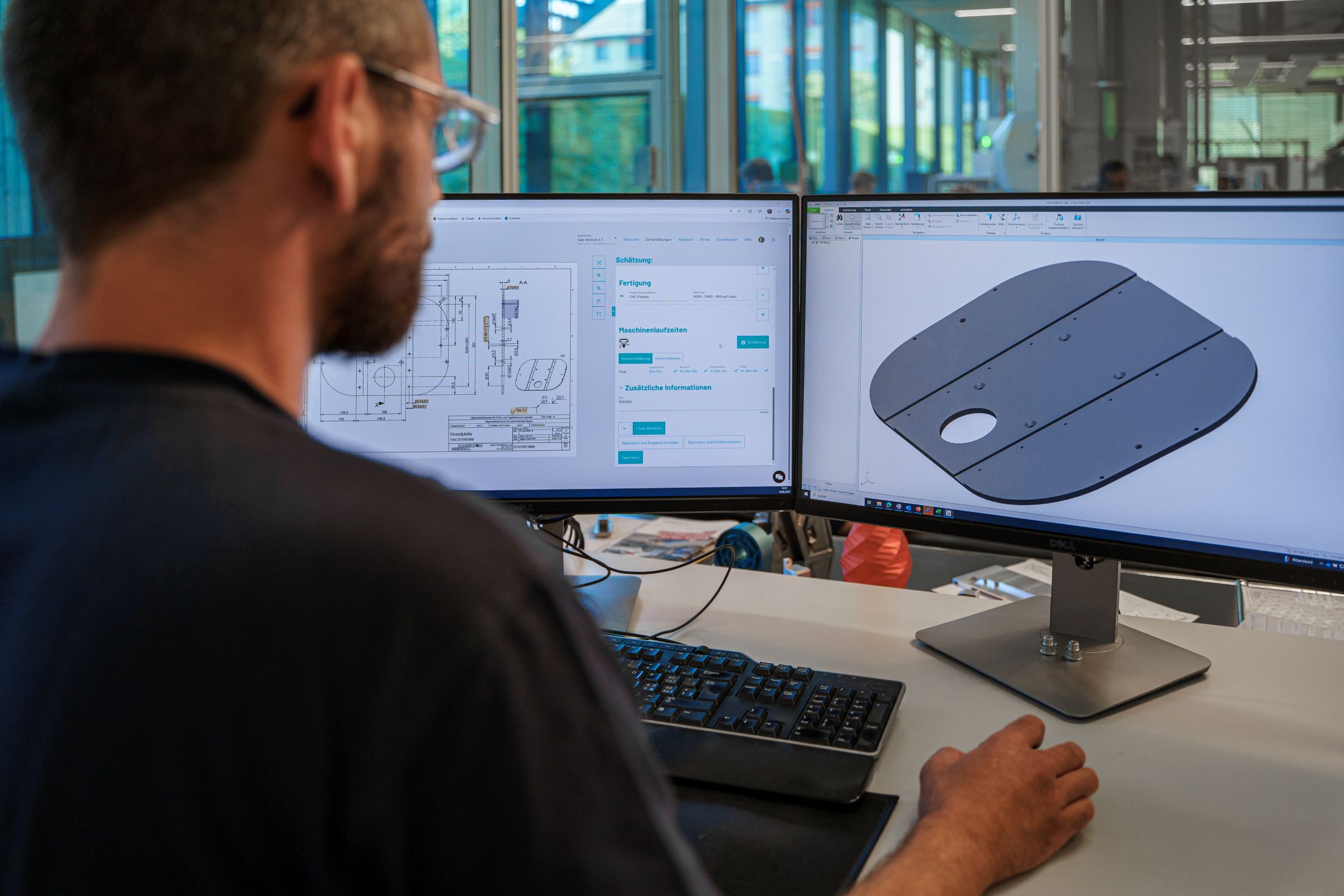
At Hamilton, prototyping has always meant working with the utmost precision – and with a strong spirit of innovation. Since early 2024, Jonas Elsa, Team Lead of Production Mechanics, and his team have been using a new digital tool: AI-based software that helps calculate mechanical prototype parts faster and more efficiently.
The result? Less manual effort, more accurate quotes – and more time to focus on what’s essential: the technical realization.
From drawing to quote – in just minutes
The process is now significantly leaner. A technical drawing is uploaded, the AI analyzes the part’s shape and complexity, and automatically calculates key manufacturing parameters:
- Programming time in the CAM system
- Setup time for the machine
- Machining time on the CNC machine
The software learns continuously – every manufactured part adds to its knowledge base. With this data, the team can quickly and reliably generate quotes, which is crucial since internal prototypes often compete with external sourcing options.
Digital support that delivers measurable value
The AI really shines on complex projects with multiple components: it dramatically reduces the time required for cost estimation and improves planning accuracy. For every manufactured part, a digital «data sheet» is automatically created – containing all relevant details for future calculations. As a learning system, the AI becomes more efficient with every use.
The advantages:
- Faster, more accurate quotes
- Greater efficiency in machine and resource planning
- Support even for small batch sizes and variant production
High-tech meets craftmanship and team spirit
Hamilton’s Production Mechanics team blends technological innovation with hands-on expertise. In addition to the AI software, their day-to-day operations include a wide range of advanced manufacturing technologies:
- CNC milling (with 3-, 4-, and 5-axis)
- CNC turning (with milling head, up to 65 mm diameter)
- Laser welding and laser marking
- Wet painting
- Quality assurance
A variety of materials are processed – from aluminum and steel to plastics and even titanium. Currently, three team members are using the new software – and interest across the team continues to grow.