Pride in our handling of the pandemic
Media report 18.02.2022The coronavirus forced many businesses to make changes. While the restrictions brought businesses in many areas to a standstill, Hamilton went into overdrive.
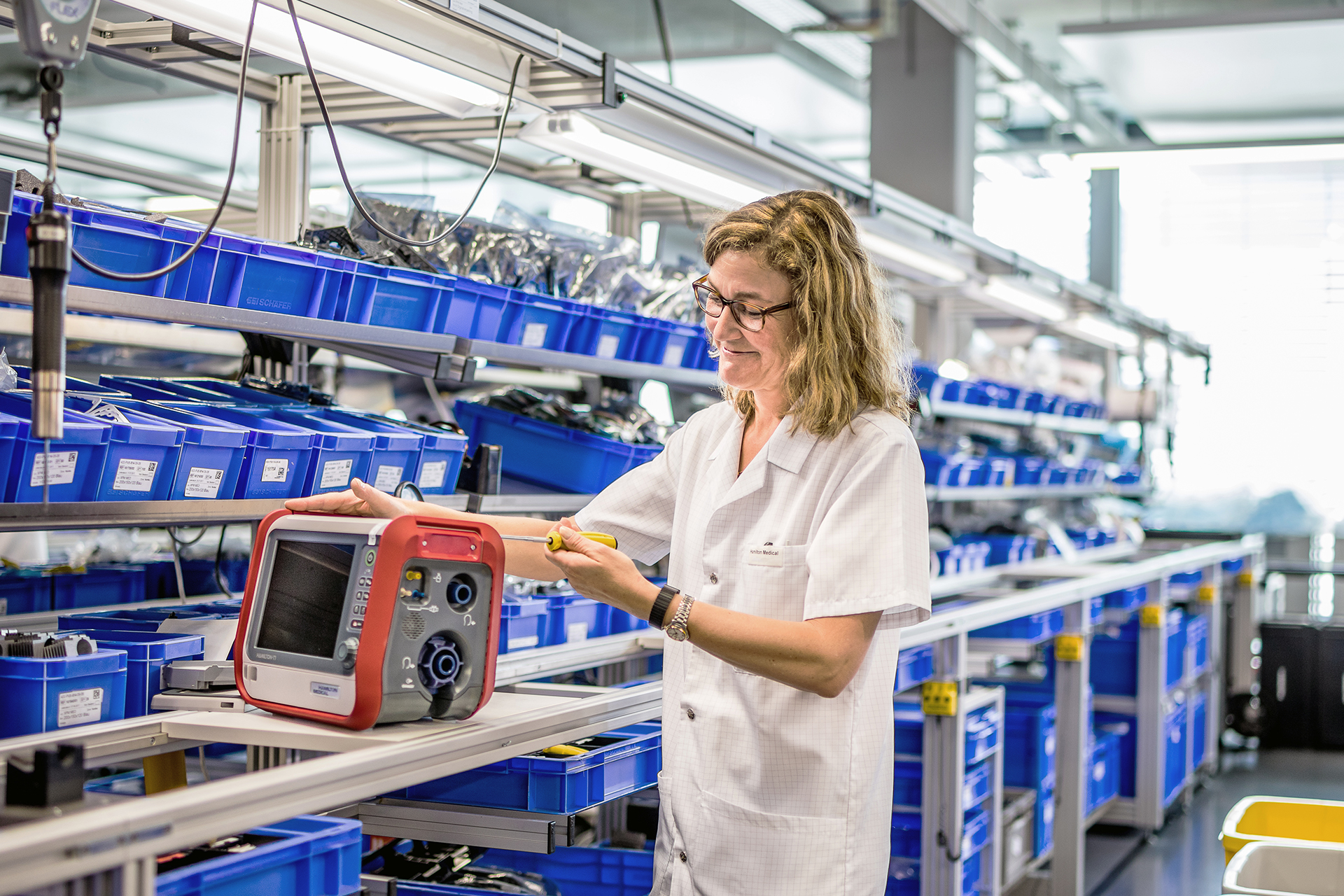
In the canton of Graubünden, Hamilton produces ventilators and PCR tests as well as sensors used in vaccine production. These are then shipped to destinations all across the globe. To meet the high levels of demand experienced during the pandemic, production had to be expanded very rapidly. This was a challenge – even for the HR department.
In the spring of 2020, the coronavirus pandemic turned our lives upside down, both privately and professionally. Many businesses had to shut down temporarily and place their employees in short-time work. But not Hamilton. During this period, it engaged in a massive recruitment drive in order to meet the rapidly rising demand for ventilators, PCR testing equipment and sensors used in vaccine production. At the end of 2019, there were approximately 1,200 employees working at Hamilton in Switzerland. Then, within a few short weeks, the company workforce had grown to 1,600 employees.
Reflecting back on that period, Gianina Viglino-Caviezel, who was Hamilton’s HR manager at the time (now CFO & Vice President Shared Services), remarks that it was a win-win situation. “We needed staff, whereas other industries were unable to allow their staff to come in to work due to the coronavirus restrictions. In this difficult situation, we were able to lend a hand.”
“We needed staff, while other industries did not – so it was a win-win situation.”
From dentists to hairdressers
In the production operation, Hamilton hired 100 staff on temporary employment contracts. They came from very diverse industries. “We had inquiries from the catering sector and industrial enterprises, as well as from dentists, a beautician and a hairdresser”, explained Gianina. “Many of them had been reading in the press about Hamilton’s contribution towards combating the pandemic and they wanted to play a part in that.” The real challenge was not finding new staff but the incredible pace of the process. The current HR manager, Daniela Gialluca, was responsible for the hiring process. “Everyone in our recruiting team was conducting five to seven interviews per day. And these were being conducted in a new fashion, since everything could now only be done digitally, even in HR. On top of that, there was the challenge of familiarizing the new staff with the production process at a time when our production operations were in overdrive.
24-hour operations
According to its own information, one out of every five ventilators used across the globe to treat coronavirus was produced by Hamilton. 60% of all major PCR test facilities worldwide were also manufactured in these production halls. And all coronavirus vaccines would be made with the aid of Hamilton sensors.
To enable this enormous amount of work to be done, the production process was completely transformed. New shifts were created – at peak periods, including nights and weekends – and, in some cases, parallel production lines were established. Staff had to be reassigned or merged into other groups. These changes were always met with great understanding. Daniela Gialluca and Gianina Viglino-Caviezel noticed a growing team spirit and excellent willingness. “Our employees felt a strong sense of pride in the fact that they were making a contribution to the world during this difficult period,” Gianina explains. To which Daniela Gialluca adds: “Everyone was mutually helping each other out. What we experienced at the human level was fantastic.” During the course of this intensive day-to-day work, our staff also shared some joyful moments, which they will not quickly forget. For example, when the Swiss Army’s Super Pumas landed next to the plant in Domat/Ems to collect the ventilators. “That spread through the company like wildfire.”
Growth remains steady
Hamilton currently employs around 1,500 permanent staff in Switzerland – that’s 300 more than before the pandemic. Demand levels are no longer quite so high now, compared with when we were fighting the pandemic. However, these employees will still be needed in the future. “We have a broad range of products”, remarks Gianina Viglino-Caviezel. “We will also be bringing further innovations to the market. We still have some in the pipeline.” Hence, we expect that Hamilton will continue to grow, including in terms of its workforce, and irrespective of pandemics. Just as the Graubünden-based company has continuously done for the past 20 years.